Optomechanical Devices
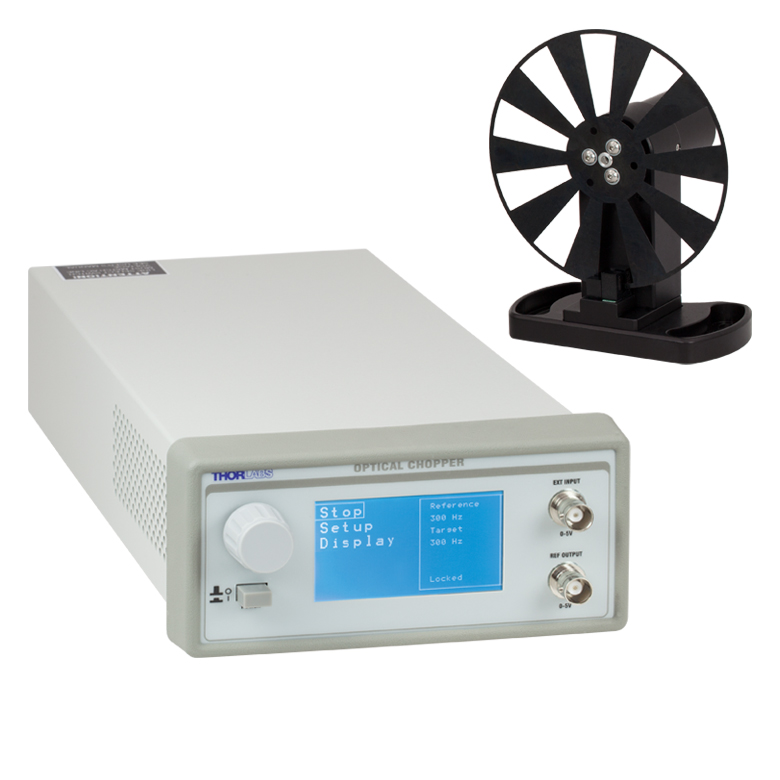
Optical Chopper System
- Crystal-Stabilized, Phase-Locked Feedback Loop Suppresses Low Frequency Drift and Phase Jitter
- Harmonic, Subharmonic, and Fractional Harmonic Chopping with Sum and Difference Reference Outputs
- Microprocessor Controlled
- Single- and Dual-Frequency Blades Available
- Harmonic Frequency Blades Available for Pump-Probe and Other Nonlinear Experiments
- Save and Recall User Setups in Non-Volatile RAM
- USB Interface
- Control Software Package Included
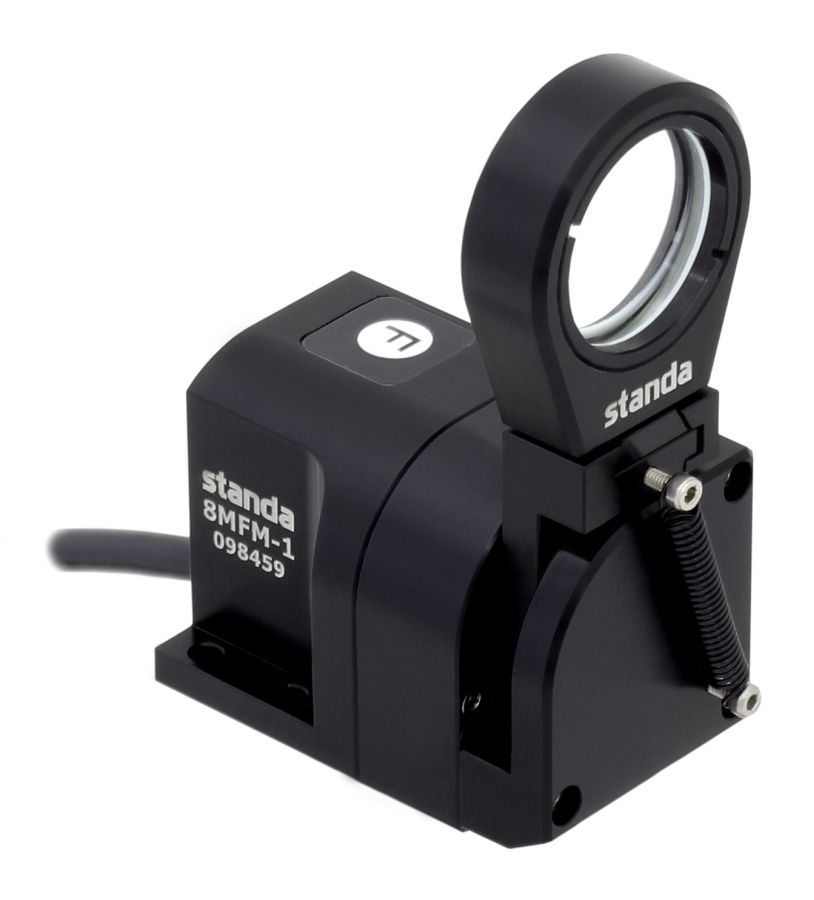
Motorized Filter Flip Mounts
- Lens Holder Included
- MFF101(/M) Includes One LMR1(/M) Ø1″ Lens Mount
- MFF102(/M) Includes One LMR2(/M) Ø2″ Lens Mount
- Compatible with All LMR Series and FMP Series Mounts up to 2.0″ Optic Diameter
- Velocity Feedback for Smooth Transitional Motion
- Mechanical Hard Stops for Repeatable Positioning
- 8-32 (M4) Tap for Post Mounting
- Flipper Unit Has Small 30 mm x 30 mm Cross Section
- Remote Handset with 39″ (1 m) Cable, APT Software Suite, and Power Supply Included
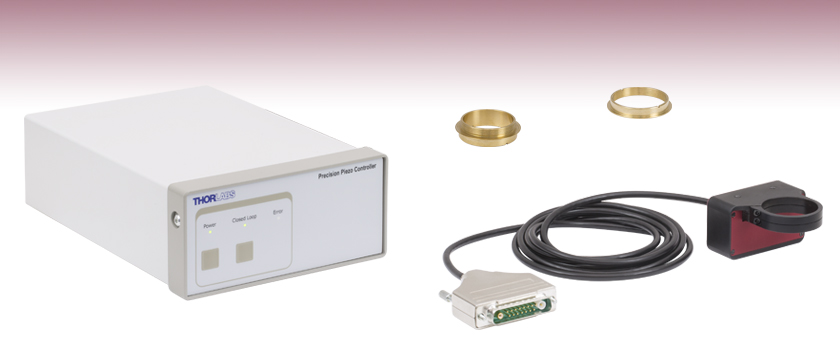
Piezo Objective Scanner
- Fast Acquisitions and High Frame Rates Enabled by 25 ms Typical Settling Time
- Maximum Clear Aperture of Ø29.0 mm Supports Large-Field-of-View Objectives
- Capacitive Feedback Sensors Provide Resolution Down to 1 nm and Help User Actively Compensate for Drift
- Quick-Release Flexure Clamps Allow Fast Objective Exchange
- Compatible with Upright, Inverted, and Rotating Microscopes
- Standalone Kinesis® and APT™ Interfaces, ThorImage®LS Integration, and Control via External Voltage
- Software Permits Easy Tuning for Different Objective Weights
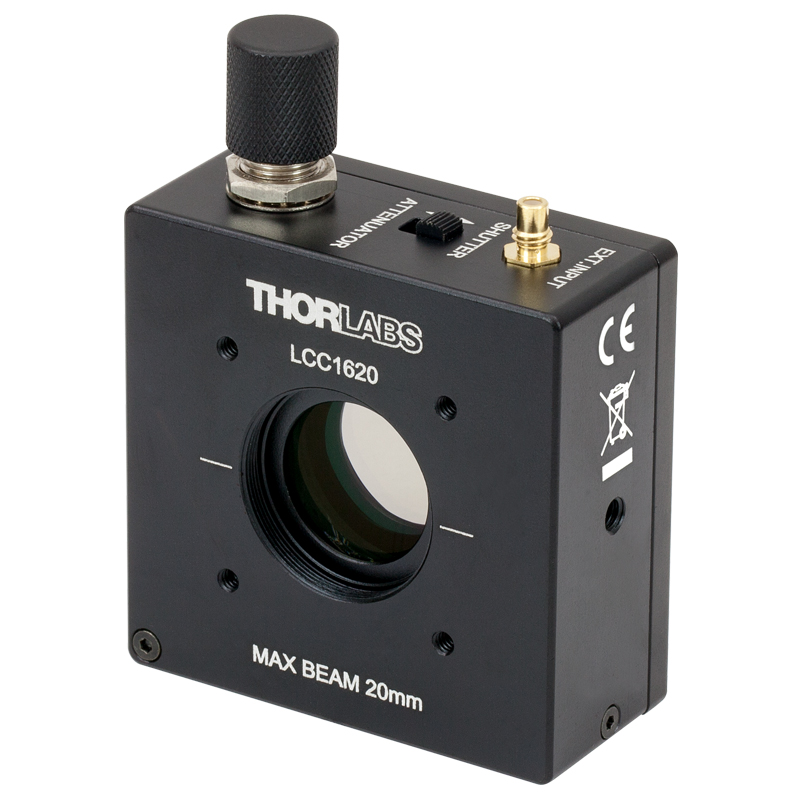
Liquid Crystal Optical Beam Shutter / Variable Attenuator
- Liquid Crystal Optical Shutter and Variable Attenuator for 420 – 700 nm Light
- Vibration-Free Device with No Moving Parts
- High Average Transmittance (>60%) and Contrast Ratio (8000:1) Over Operating Wavelength Range
- Shutter and Attenuator Modes
- Fast Shutter Switching Speeds (Shutter Mode):
- Opening: 5 ms
- Closing: 1 ms
- Post Mountable and 30 mm Cage System Compatible
- SM1 (1.035″-40) Threaded for Compatibility with Lens Tubes
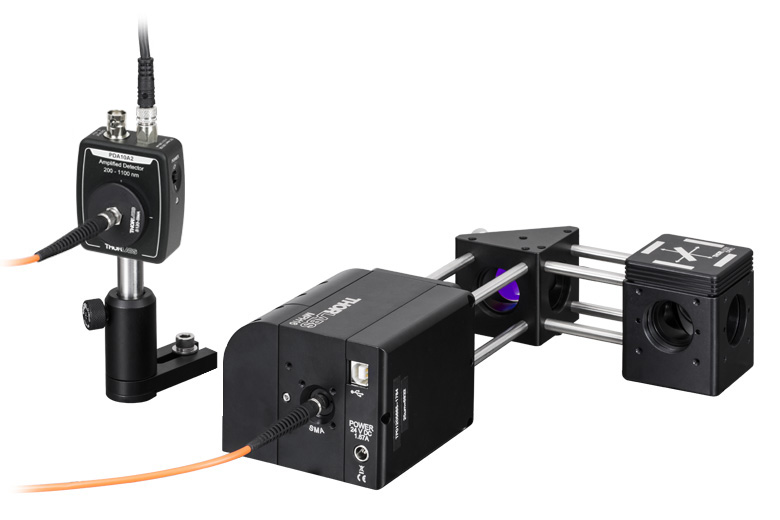
Motorized Pinhole wheel
- 16 Pinhole Sizes: Ø25 µm to Ø2 mm (See the Specs Tab for Details)
- Quick and Repeatable Pinhole Positioning
- Free Space Input Compatible with 30 mm Cage Systems (Using Dovetail Adapter)
- Fiber-Coupled Output with SMA Connector (Use Ø400 – Ø1000 µm Core MM Fiber)
- Compatible with 16 mm and 30 mm Cage Systems